More With Less: Sustainability Through Pre-Fabrication
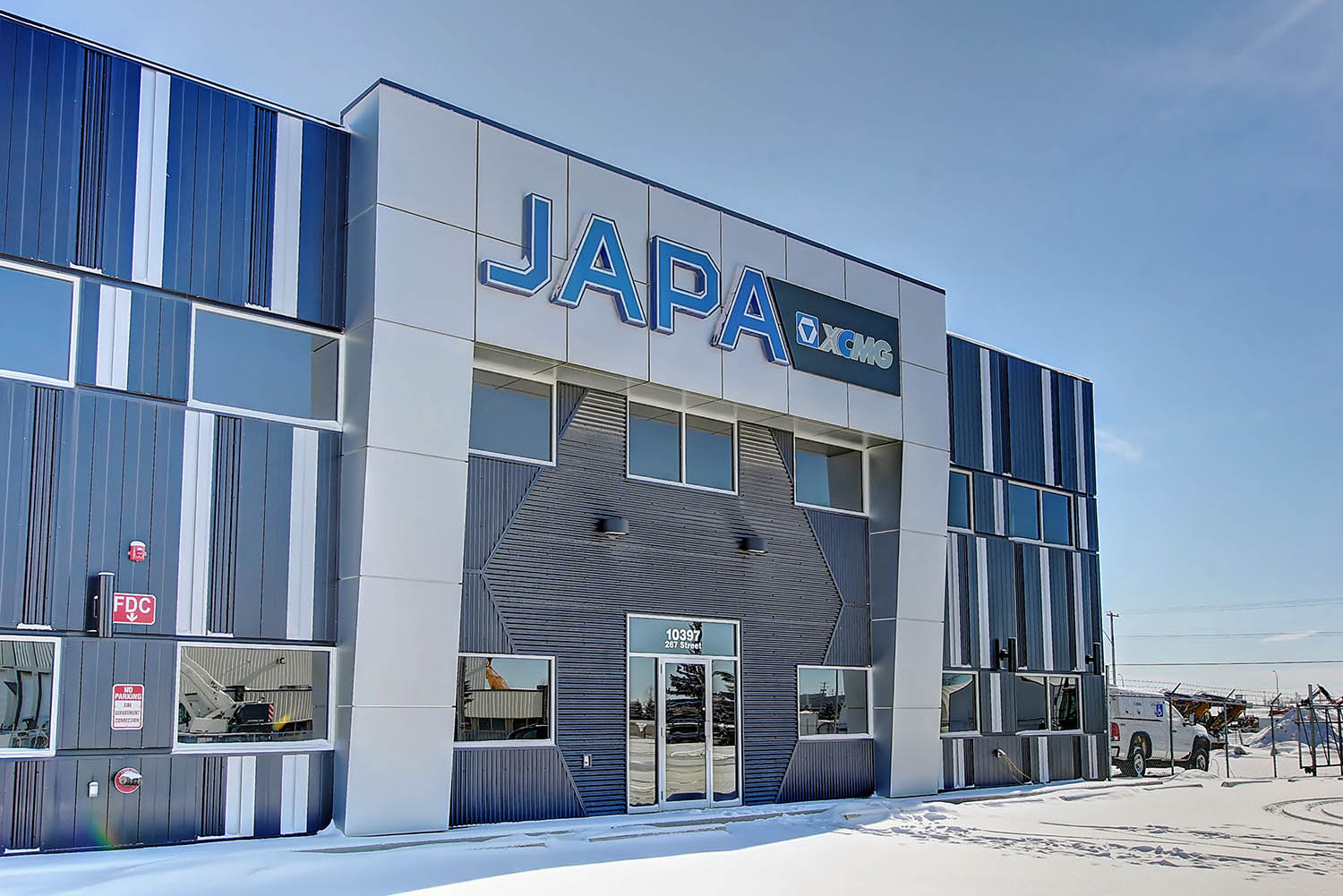
Besides labour, materials will be at the forefront of any construction budgeting. How can you reduce both? To answer this, we have to look both back to the past, and forward to what a build in the future might look like.
Canada is no stranger to pre-fabrication. While pre-fabrication has recently re-emerged in terms of saving materials and labour costs, it originated to fill a housing need during interwar years. For years, even Sears catalogues sold houses that were “already cut and fitted,” meaning homeowners could assemble the walls and floors on-site after the pieces were constructed and shipped from elsewhere.
Much has changed in terms of materials and technique, but the principles remain the same. Through design builds today, pre-fabricated commercial and industrial buildings not only stand tall but also stand the test of time.
As you stay ahead of the curve in your business, Flynn Bros Projects is consistently exploring new partnerships with manufacturers who help bring affordability, customization, and sustainability into your commercial design build project.
Construction Materials: Now vs. Then
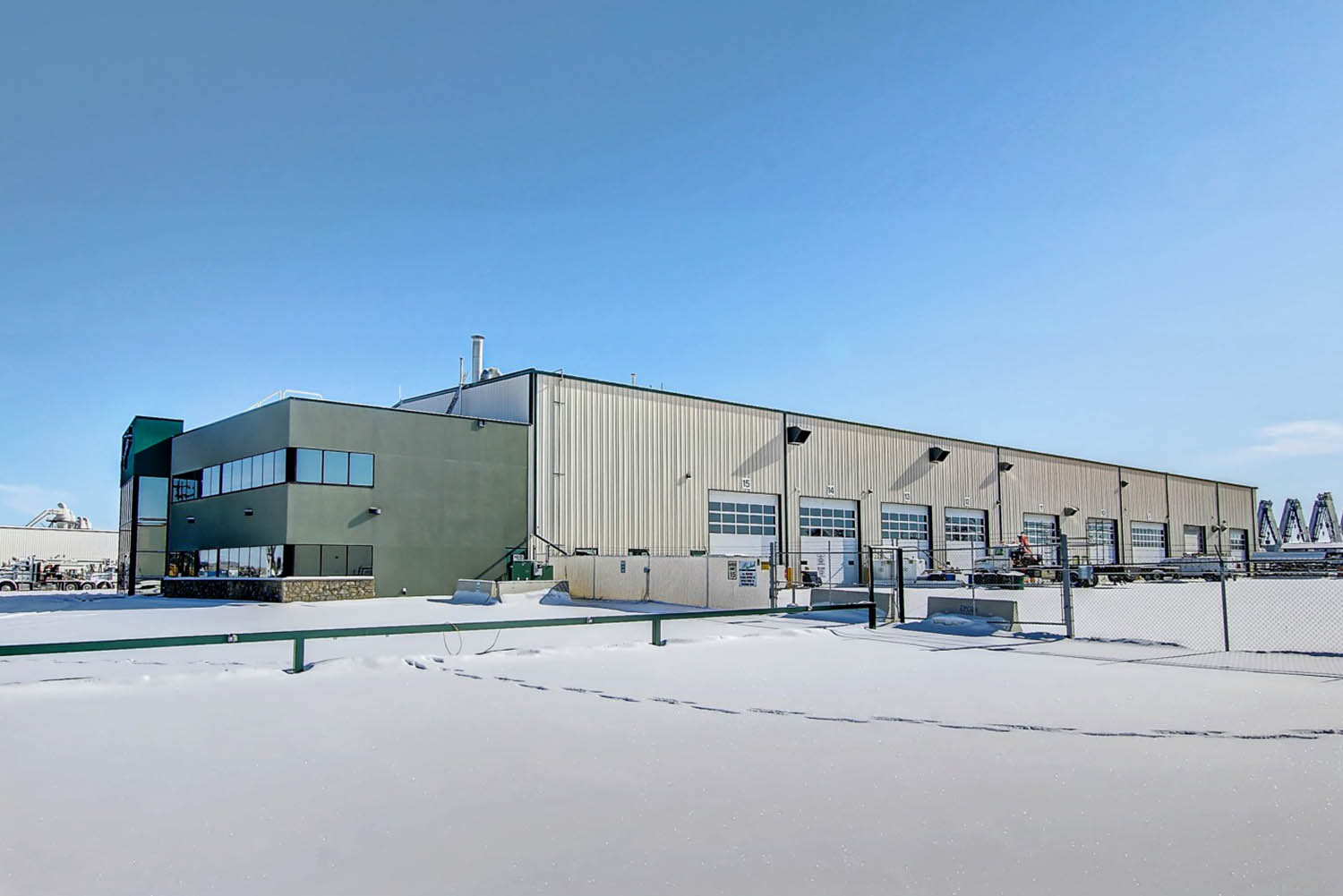
The history of construction materials has been an evolution. Even structural wood and timber have grown past their origins as resilient plant fibres through pressure treatments, composites, and laminates. So too, is steel and concrete evolving.
The need for diversification beyond traditional and often unsustainable materials has never been more discussed. However, to balance the intense structural demands of commercial and industrial builds while retaining customizability and cost-efficiency, our process often asks how we can use materials better.
Like decades ago, pre-fabrication once again answers a need unique to our time.
Pre-Fabricated Building Materials
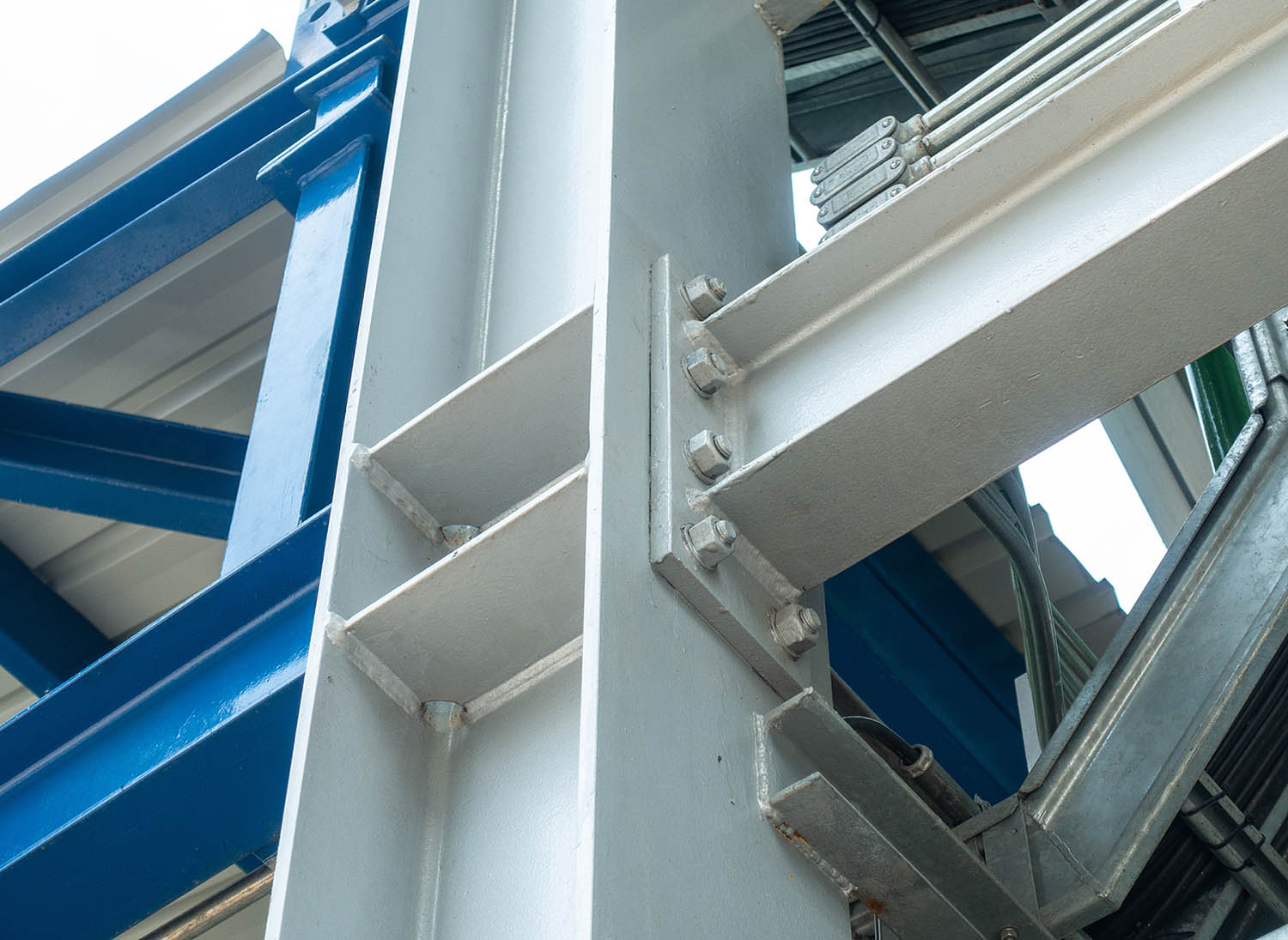
Pre-fabricated building materials offer many benefits, starting with reduced waste. Designing pre-fab structures means that every piece of material serves a specific function, minimizing leftovers that can contribute to environmental waste. Our partnerships with experts who specialize in manufacturing these pre-fab components ensure that your new build project is a seamless whole where every piece fits perfectly into place.
The customizable nature of pre-fabricated materials also allows for a high degree of flexibility in design, both aesthetically and in terms of purpose. Every business is unique, and our commitment to customization means that your commercial space can reflect the identity and vision of your company while still maintaining the cost and environmental benefits of pre-fabrication.
Your project manager will work with you to accommodate any unique needs you may require, and we can help orchestrate high-efficiency technologies into the very backbone of your build. We keep our project manager-to-job ratio low so we can understand and anticipate your exact expectations on what success looks like.
Regulatory and Safety Considerations
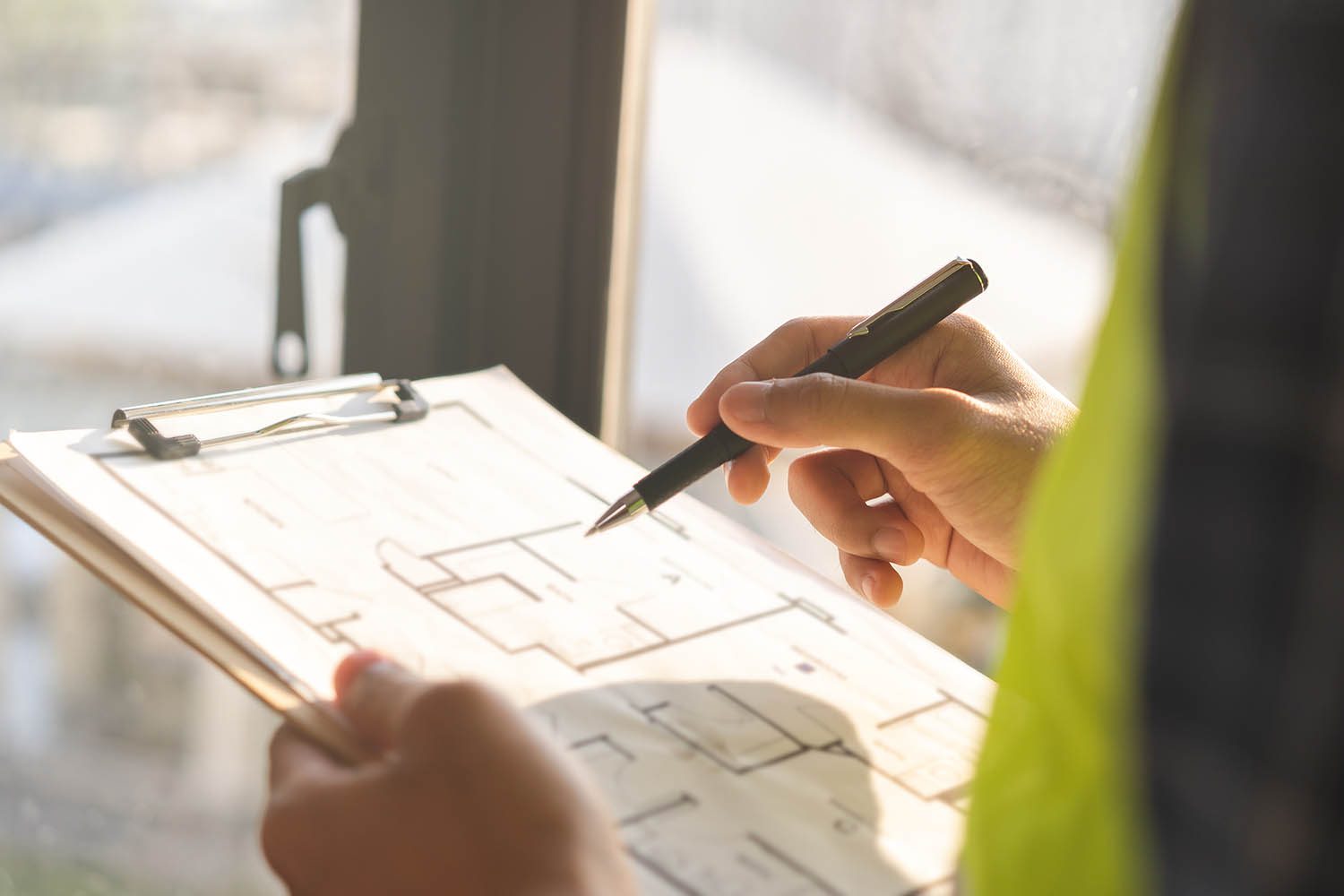
If you’ve found yourself lost in the web of building codes and regulations, you’re not alone. During pivotal moments of growth, the last thing you need is a delay that sets you and your budgeting back. Our materials, suppliers, and construction methods comply with regulatory standards, ensuring that your project is not only legally sound but also safe and durable.
Additionally, we offer fabrication services in-house to meet the challenges that face any large project. With the right eyes on every step of the process (including those big-picture brainstorms where we first envision your build), you can rest assured that pre-fabrication doesn’t skip any of the steps on the way to the final walk-through.
Weather-Proofing Your Pre-Fabricated Building
Alberta is no stranger to extreme weather conditions, and we are well aware of the unique challenges posed by our prairie climate.
The materials and methods we use are designed to handle the rigours of extreme weather. In fact, many builders are choosing pre-fabrication as an affordable option for conditions ranging from arctic circles to deserts—between which is a temperature range Alberta experiences each year.
Whether it's extreme cold or sudden temperature fluctuations, you can trust that your design build has been weather-proofed to ensure longevity and structural integrity, ensuring business continuity even while the cities slow to a halt.
In our experience, business growth doesn't wait for favourable weather. Our expertise in construction during weather events means that your expansion plans are not stuck waiting for sunnier days—your business can thrive at any time of the year.
Conclusion
The future of construction is here through pre-fabrication. With the right partnerships in design and project management, it's an affordable, customizable, and sustainable way to grow your business and plan for the long term.
As we conclude this short exploration of contemporary construction, one should remember the untapped potential of pre-fabricated buildings. Flynn Bros Projects is committed to infusing our manufacturing, project management, and design expertise into any low-cost, fast-building structures you can imagine—above all, one that won’t sacrifice the aesthetic side of your brand and values.
Ready to embark on your journey beyond steel and concrete? Contact Flynn Bros Projects for your next design build, expansion, or grain handling system. Together, we can build a space that meets your needs today and sets the stage for your long-term success.
Stay Connected with Us!
Follow us on our social media channels to get the latest updates, exclusive offers, and behind-the-scenes content. Join our community and be part of the conversation!