Proactive Maintenance: Ensuring the Longevity of Your Structures
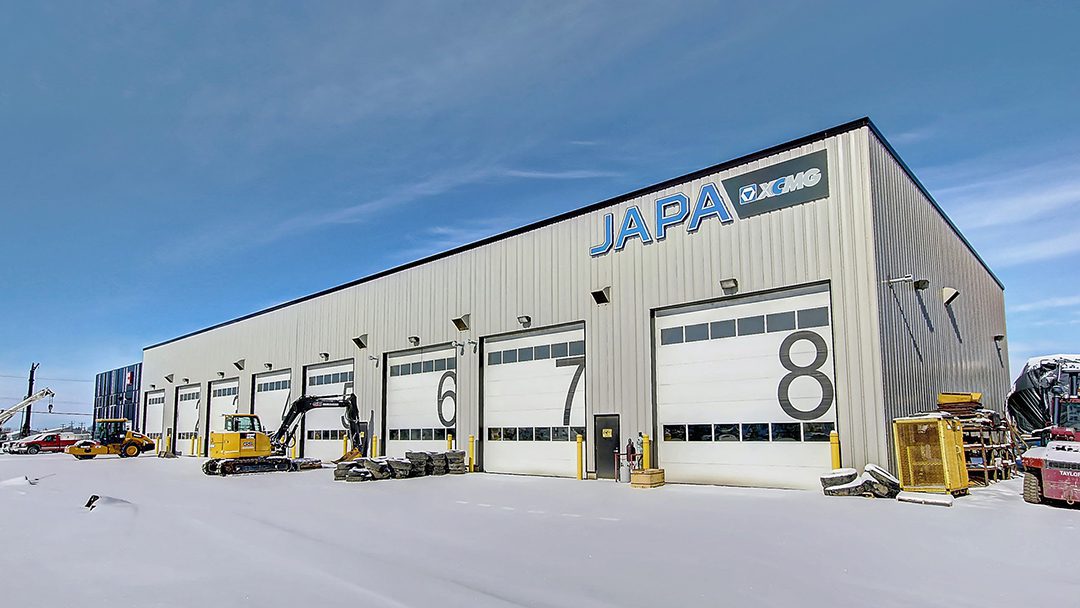
When it comes to construction and infrastructure, the importance of maintenance cannot be overstated. Proactive, regular maintenance is the cornerstone of building longevity, safety, and functionality. At Flynn Bros Projects, we understand that taking care of what you’ve built ensures that it continues to serve its purpose—efficiently and safely—year after year.
Why Maintenance Matters
Neglecting maintenance is like skipping oil changes in a car—it might not show immediate effects, but over time, the damage becomes apparent. Buildings are no different. Regular upkeep not only preserves the structural integrity of your assets but also reduces the likelihood of costly repairs or replacements. Proactive maintenance extends the lifecycle of your building and helps avoid unnecessary expenses.
Key Maintenance Practices

Different types of buildings require tailored maintenance strategies. Here are some essential practices Flynn Bros Projects recommends:
Industrial Buildings
- HVAC System Maintenance: Regularly clean and replace air filters and schedule annual inspections to maintain energy efficiency and air quality.
- Plumbing: Address leaks promptly, clear drains, and ensure water heaters function optimally.
- Lighting Systems: Upgrade to energy-efficient lighting, routinely replace bulbs, and clean fixtures to improve brightness and reduce energy consumption.
- Elevators and Escalators: Conduct routine safety inspections and ensure compliance with safety regulations.
- Fire Safety Systems: Regularly test alarms and sprinklers, and maintain emergency signage and extinguishers.
Agricultural Buildings
- Roof and Gutter Maintenance: Prevent leaks by inspecting roofs and cleaning gutters to ensure proper water drainage.
- Structural Inspections: Address wear and tear in storage facilities and barns, focusing on support beams and foundations.
- Ventilation Systems: Maintain airflow by cleaning fans and ducts to prevent moisture and mold buildup.
- Pest Control: Schedule regular pest inspections and implement treatments to protect equipment and inventory.
Flynn Bros Projects: Supporting Your Maintenance and Upgrade Needs
At Flynn Bros Projects, we understand that maintaining and improving your facilities is key to keeping your operations running smoothly. Whether you need targeted maintenance or strategic upgrades for your grain storage systems or commercial buildings, our experienced team is here to help. We provide solutions designed to enhance functionality and extend the lifespan of your infrastructure, all while minimizing disruption to your business.
Success Stories

One of Flynn Bros Projects' notable successes involved the reconstruction of a commercial facility for Canadian Agri-Blend after an interior fire caused significant structural damage. While the building's foundation remained intact, large portions of the pre-engineered structure needed replacement.
Flynn Bros worked closely with engineers to overcome challenges like adjusting anchor bolt locations and reinforcing an adjacent building's roof structure to handle additional drift loading. The team doubled up purlins and bolted reinforcements to the main rafter—all while ensuring Canadian Agri-Blend could maintain operations throughout the rebuild. This project highlights the critical role of timely maintenance and repairs in preserving business continuity and ensuring long-term structural integrity.
Future Trends in Construction Maintenance
The construction world is evolving, and maintenance practices are keeping pace with innovations:
- Smart Maintenance Systems: IoT devices and AI monitor systems in real time, sending alerts for potential issues before they escalate. These technologies help prevent failures, optimize performance, and reduce long-term maintenance costs.
- Advanced Predictive Maintenance Techniques: Data analytics and sensor technology are revolutionizing maintenance by identifying potential issues through usage patterns and equipment performance. Predictive maintenance minimizes downtime and extends the lifespan of critical infrastructure. Flynn Bros Projects integrates these advanced techniques to ensure reliability and efficiency for their clients.
- Integrated Management Systems: Centralized dashboards provide a comprehensive view of maintenance requirements, streamlining processes and improving coordination across teams
At Flynn Bros Projects, we are committed to staying ahead of the curve. Our team continuously explores new technologies and methods to ensure our clients receive the best care for their investments.
Conclusion: Take Action Today

Proactive maintenance is an investment in your future, ensuring that your buildings and structures remain assets rather than liabilities. Flynn Bros Projects is here to help you navigate maintenance challenges with expertise and precision.
Let’s protect your investment together. Contact Flynn Bros Projects today to discuss
Stay Connected with Us!
Follow us on our social media channels to get the latest updates, exclusive offers, and behind-the-scenes content. Join our community and be part of the conversation!