How Design-Build Construction Streamlines Project Delivery
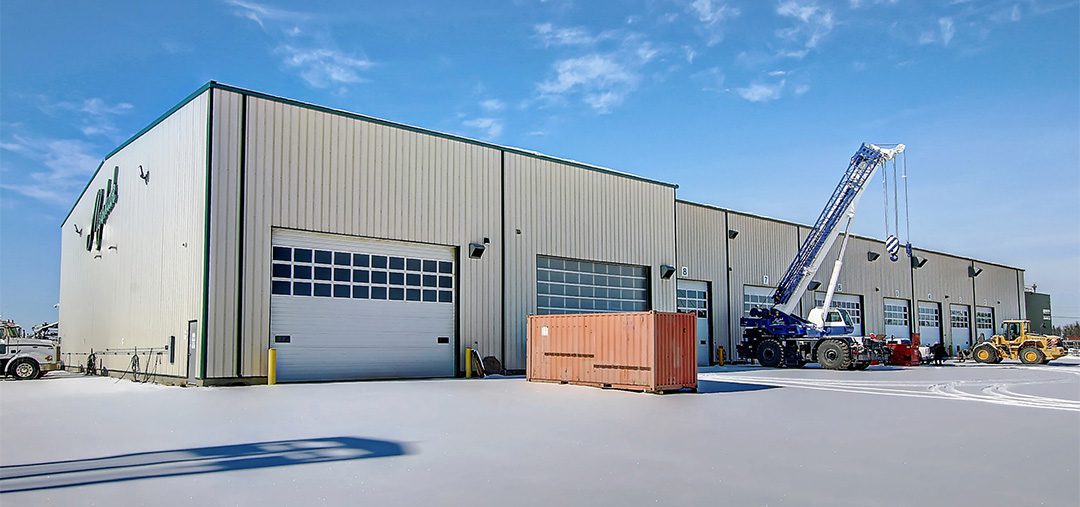
Measure twice, cut once—that’s how the saying goes. Nowadays, it applies to a lot more than just material costs.
Construction companies are grappling with a host of challenges, from supply shortages and high rates to a lagging labour market. Even once-predictable cost metrics like general labour have seen significant increases. This new budgeting reality has pushed many companies to rethink their strategies for timely and budget-friendly project delivery.
So what can be “cut,” let alone twice? Poor materials will cost the client and the builder in reputation later on. Unskilled labour will cause similar problems, especially in delicate retrofit projects.
With that in mind, measuring twice is the best time-saver there is. And there is no more precise measurement than pre-fabrication—a highly flexible and affordable building solution that relies on maximizing productivity through efficient material use and fast construction.
Our excellence through design builds isn’t just limited to using pre-fabrication. Today, we’re sharing three reasons why design builds streamline project delivery without cutting corners.
Accuracy & Project Clarity From the Beginning
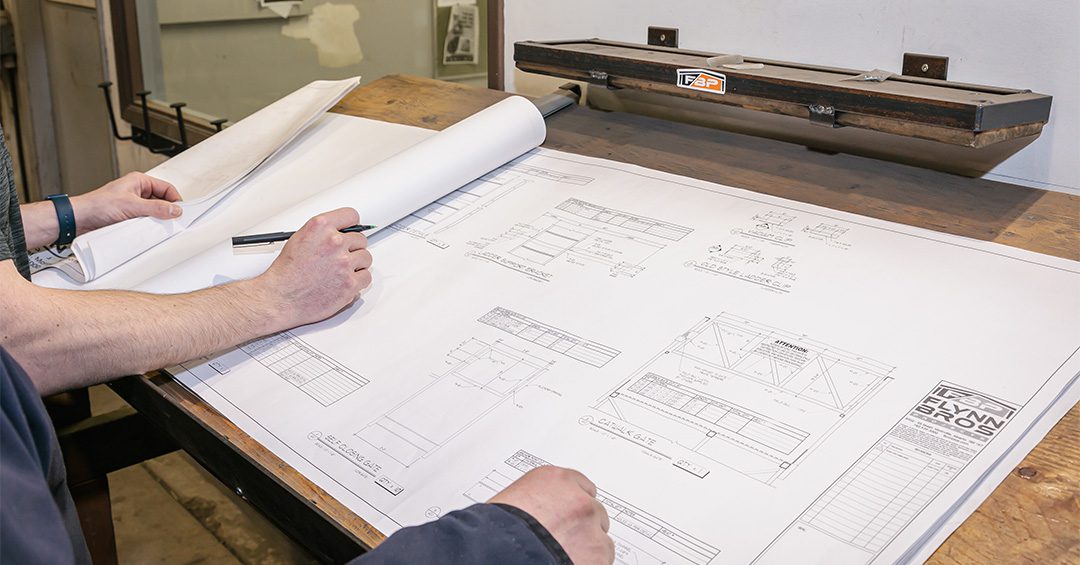
Design builds eliminate the back-and-forth communication between clients, external architects, and over-stretched builders that you may have come to expect with traditional builds. The inherent collaboration integrates you directly into the design phase from the moment you sit down with us, ensuring your vision is accurately reflected in the project blueprint. This minimizes the risk of miscommunication and expensive change orders later in the process.
Our mission is that you receive a clear understanding of project design, budget, and timeline from the outset, along with a dedicated project manager who can update you anytime. For you, that means no phone trees to navigate and no egos to fight along the way.
Pre-Fabrication for Faster Builds
Like many commercial and industrial buildings, design builds leverage pre-fabrication to expedite construction and minimize costs. Walls, roofing, or entire building sections are constructed off-site in a controlled environment. This eliminates on-site delays caused by weather or material shortages, resulting in a significantly faster build time and fewer local costs. Most importantly, your project is completed sooner, allowing you to occupy your new space or open for business quickly—something that is especially important Albertan builders who may face delays during winter weather.
In-House Regulation Expertise
Navigating Alberta's building codes and regulations can be complex, especially if you are working with multiple teams focusing on individual goals. Design-build offers the advantage of in-house project managers with decades of experience in navigating local regulations. We oversee the permitting process and ensure your project adheres to provincial safety and construction standards prior to you investing in breaking ground. This eliminates the need for separate and costly consultants, saving you time and money while guaranteeing your project's compliance.
Working With a Smaller In-House Design Team
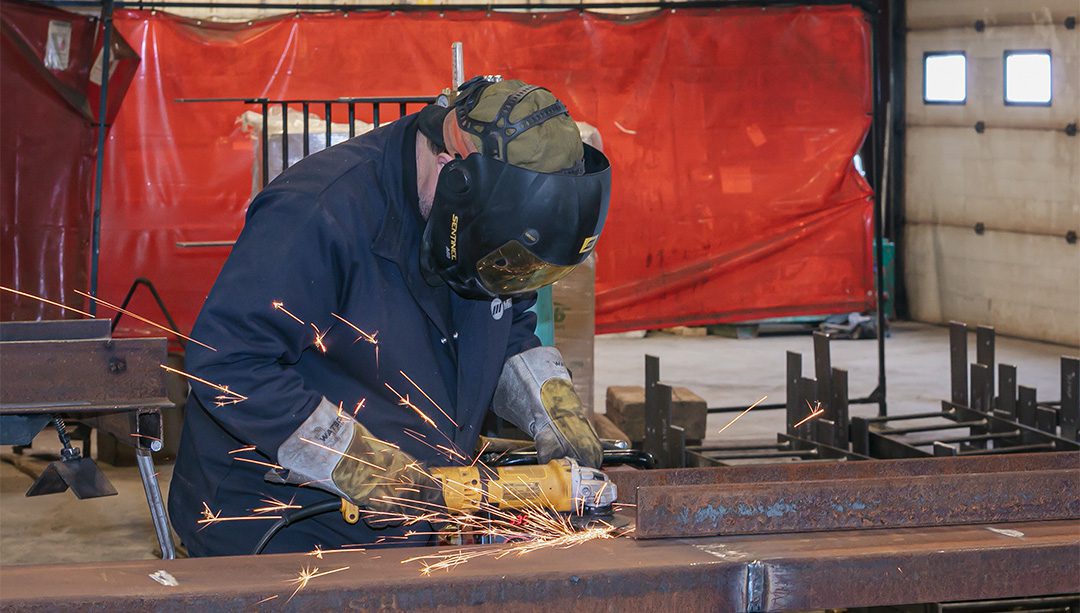
Design-build simplifies the process by utilizing a dedicated in-house design team. This eliminates the need for you to coordinate with a large team of external architects, engineers, and project managers, each with potentially competing priorities. Our close-knit team works with consistent, reliable professionals and can update you accordingly in one call rather than five. Your stakeholders will appreciate the consistent communication and collaboration, ensuring everyone is focused on achieving the most important single goal: delivering your project on time and within budget.
“Do I need an architect for my commercial building?” Not always. Professional Involvement Standards mean an engineer can often sign off on projects without a dedicated architect. This means going with professionals like Flynn Bros saves you an extra step along the way that other builders might unfairly push as a “necessity.”
Streamlining Your Commercial Build With Flynn Bros Projects
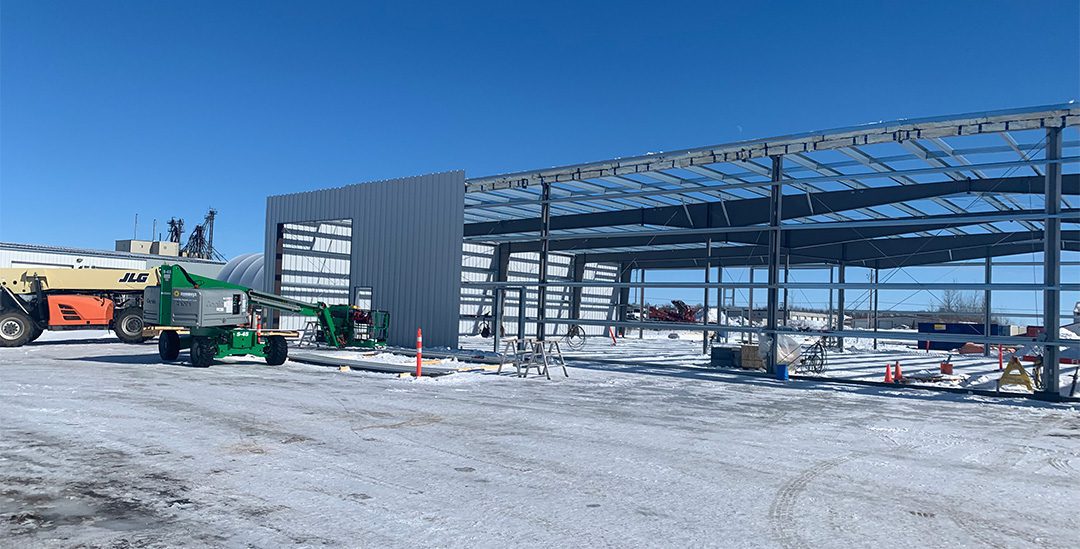
A long-term view of working efficiency and new technology in our grain handling landscape shows us how change can often be for the better. From real-time monitoring of grain conditions to increasing capacity for quicker loading/unloading, efficiency starts with a thorough look at how you store your grain and get it to market more competitively.
To start the discussion, give us a call. It doesn’t have to be a building, a bin, an elevator, or a structural project like anything we’ve done in the past. Flynn Bros Projects are proud, innovative thinkers—if you’ve got a problem, we’re here to help you solve it.
Stay Connected with Us!
Follow us on our social media channels to get the latest updates, exclusive offers, and behind-the-scenes content. Join our community and be part of the conversation!