How Grain Handling Systems Help You Hack Productivity
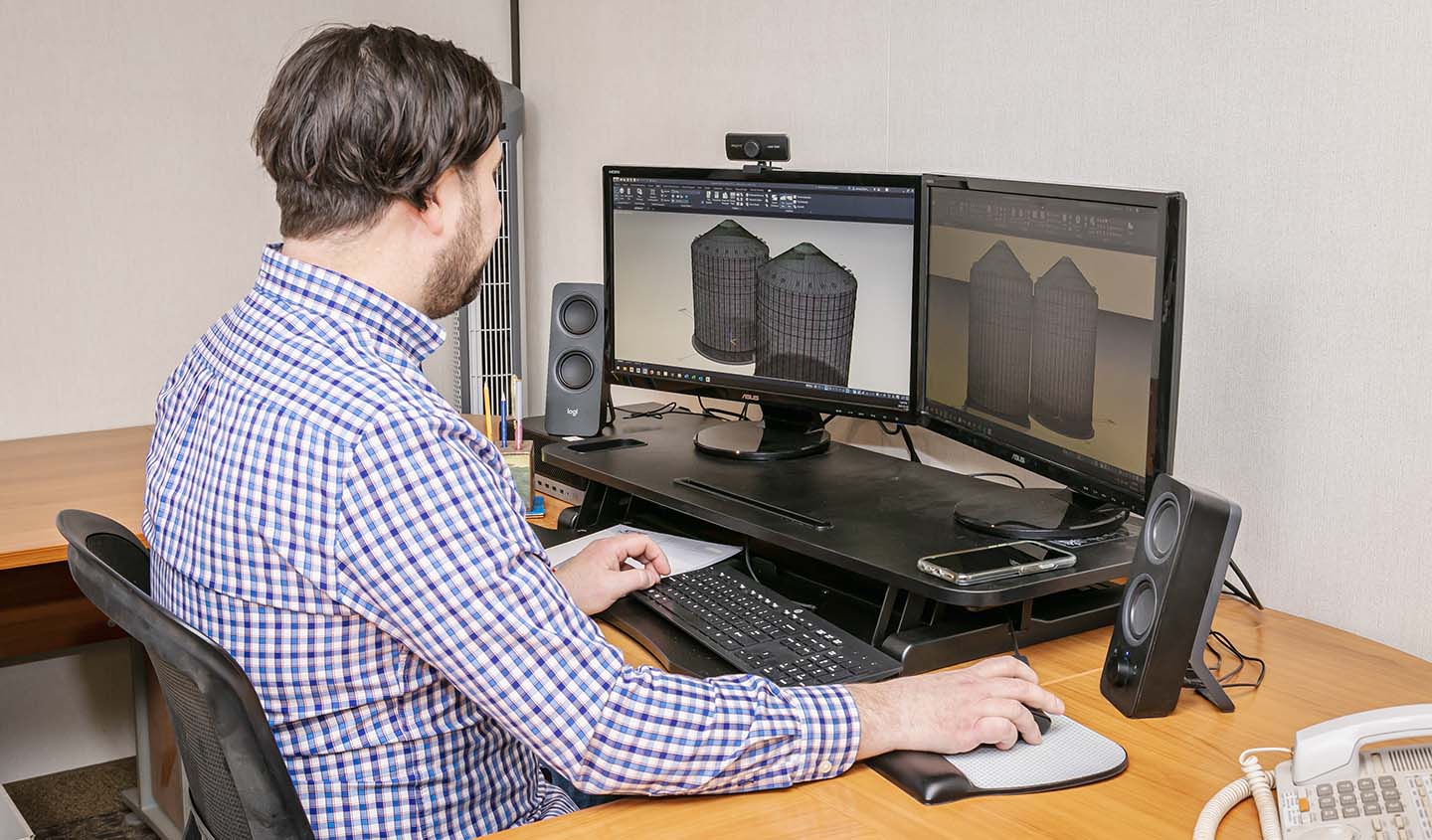
There’s no doubt about it—agriculture is hard work. Even ignoring the long hours in uncertain weather, the job is made all the more complicated by how entire batches of even shelf-stable grains like barley and wheat can be ruined at the last moment by improper storage and handling.
Canadian grain production is a competitive industry challenged by rising environmental and economic pressures. Efficiency is key, and while you perfect your craft in the field, we’ve been changing agricultural futures through robust grain handling systems. When you consider the staggering losses of up to 50% due to poor after-harvest conditions, it’s easy to see that storage and handling are two sides of the same coin.
If you’re frustrated by grain spoilage and stagnant profits as you wait to offload to market, read ahead for our take on how upgrading your storage and grain handling systems can be a game-changer—minimizing losses, boosting overall efficiency, and getting your product to market in its prime.
The Chemistry of Grain Spoilage
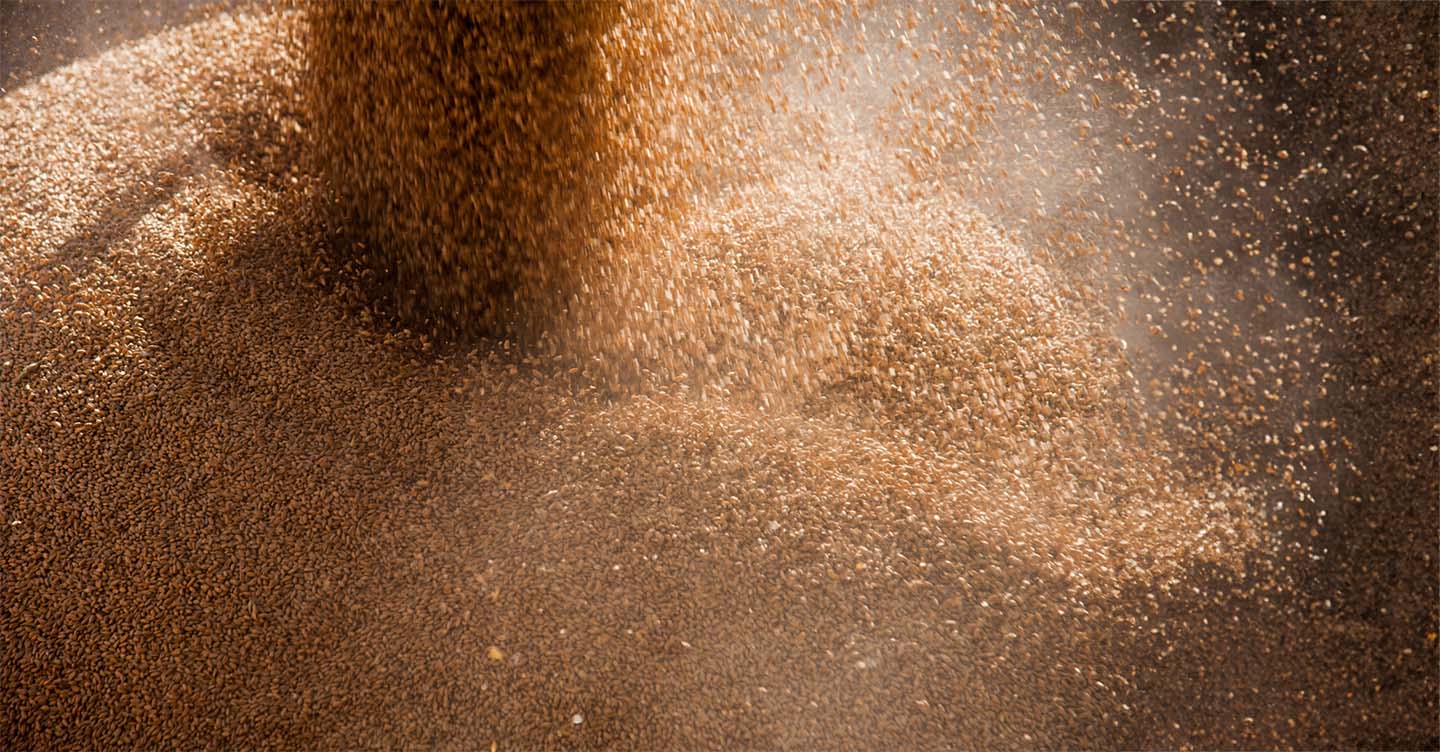
Preventing spoilage is the cornerstone of any grain handling strategy. Luckily, while some loss is inevitable, much is preventable when favourable environmental grain storage conditions are exceeded.
The hard reality is that in many cases, the prevalence of specific mold at harvest (often due to humid conditions during reaping) means that the damage to the grain has already been done. The same goes for seed hull damage that occurs as the grain is processed. Between field molds, fungi, and storage molds, you have about 7 days until total spoilage in a silo. Temperature and humidity control are essential in working within these timelines, especially as moisture content creeps up.
A rudimentary venting system may not be enough since hot air will migrate throughout your silo and cause moisture buildup in unseen areas. A striking example of this is in fall and winter conditions. As air temperature cools down around October, the grain nearest to the bin wall cools more quickly than the rest of the stored grain. This difference in temperature causes air to move down the bin wall and toward the centre of the bin. As this chilled air moves through the grain, it becomes warmer and picks up traces of moisture from the grain. When this newly warmed air hits the cool upper surface of the grain, condensation (and mold) are formed—also known as a productivity and revenue killer.
By upgrading your grain storage system, you can overcome the challenges posed by environmental conditions and see greater returns on your efforts. Better yet, by upgrading multiple silos, you can ensure each bulk grain product is kept in ideal conditions.
The Consequences of Failing to Invest in New Grain Storage Systems
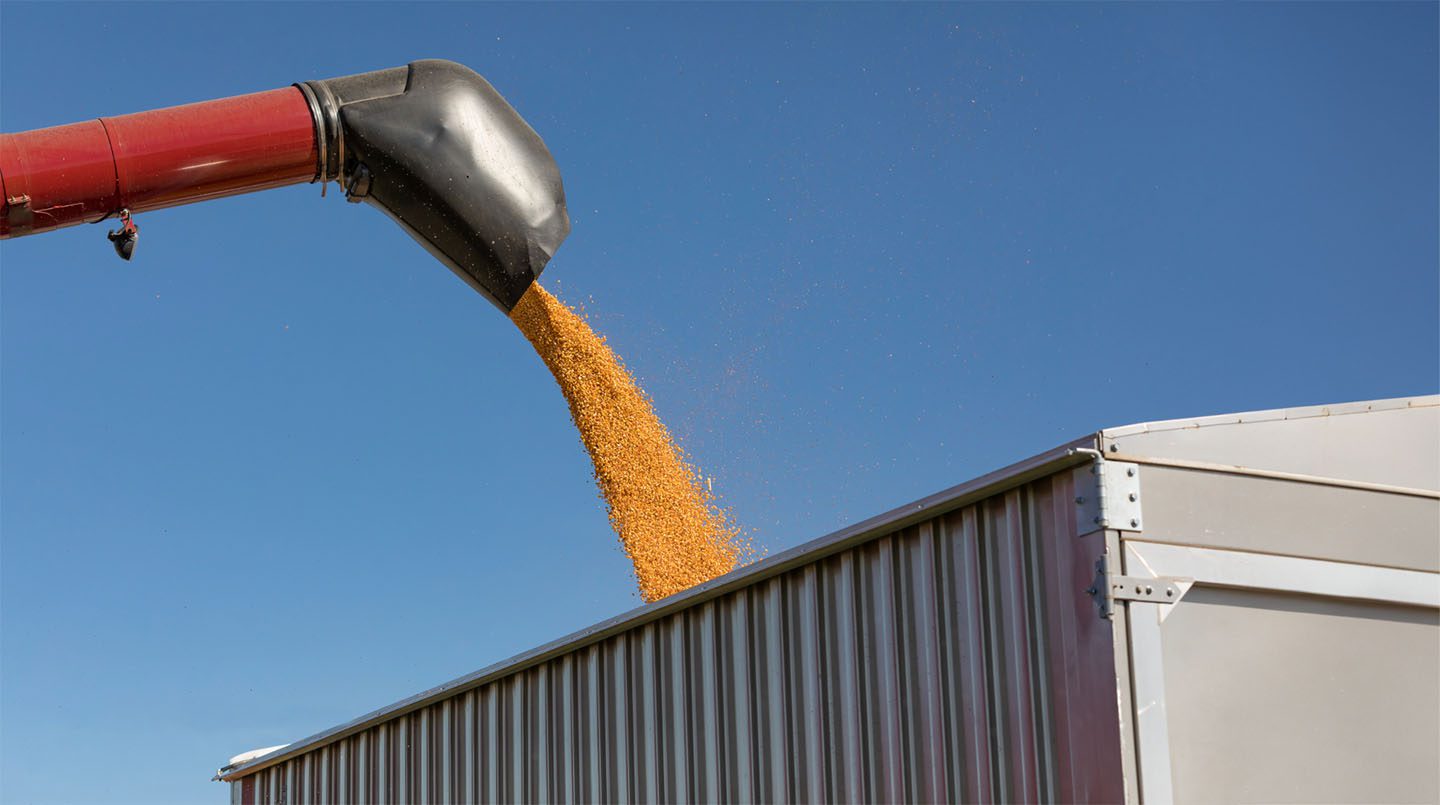
Every minute your grain sits in storage is a minute it's susceptible to spoilage. Inefficient handling systems (or outdated ones) can create bottlenecks, forcing you to hold onto your product longer. This extended storage time increases the risk of mold growth, insect infestation, and overall grain degradation, each of which directly impacts your bottom line.
Sometimes, doing things the old way is best (but maybe not this old). Today, investing in a modern grain handling system allows you to capitalize quickly, efficiently, and predictably. Swift and reliable movement between your many operations minimizes the time grain spends in storage, significantly reducing spoilage risk and pest pressure.
By prioritizing speed and efficiency with a modern grain handling system, you can safeguard grains from spoilage and leverage them as a commodity quicker, neatly boosting your revenue and export potential. Consider our work with expanding the Westlock Terminals Grain Cleaner—a testament to how upgrading at the right time can transform your operations.
Working With a Reliable Local Contractor
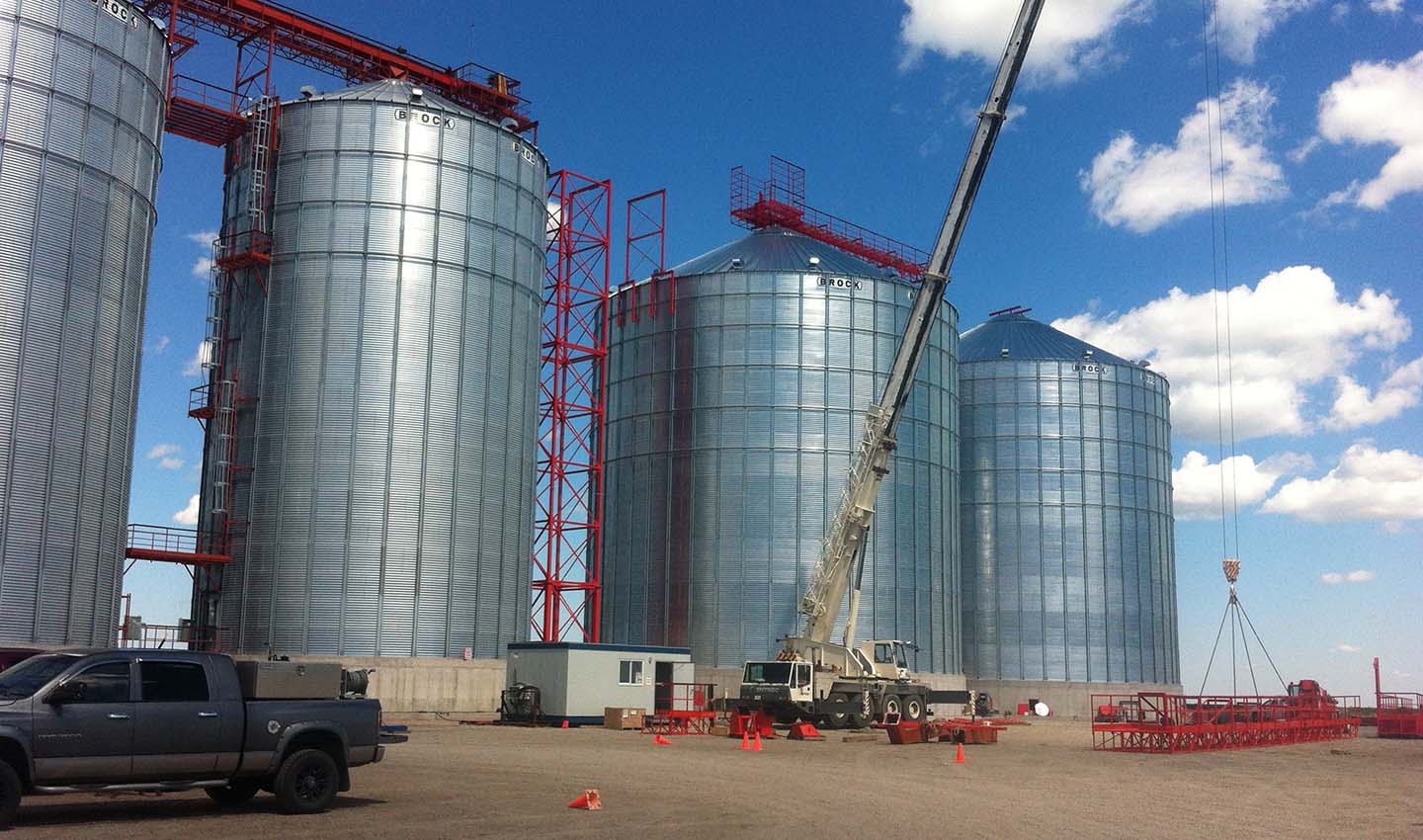
Stressful timelines don’t apply to only the grains themselves. Sometimes, the teams you hire to complete infrastructural builds are even more temperamental.
We understand. As an experienced manufacturing team for commercial grain, malt, and canola distributors across western Canada, your timeline becomes our priority. Our down-to-earth teams strive to provide you reliability after the challenge of a season well-worked. For designing, building, and servicing your grain handling systems in Alberta and beyond, contact Flynn Bros Projects today.
Stay Connected with Us!
Follow us on our social media channels to get the latest updates, exclusive offers, and behind-the-scenes content. Join our community and be part of the conversation!